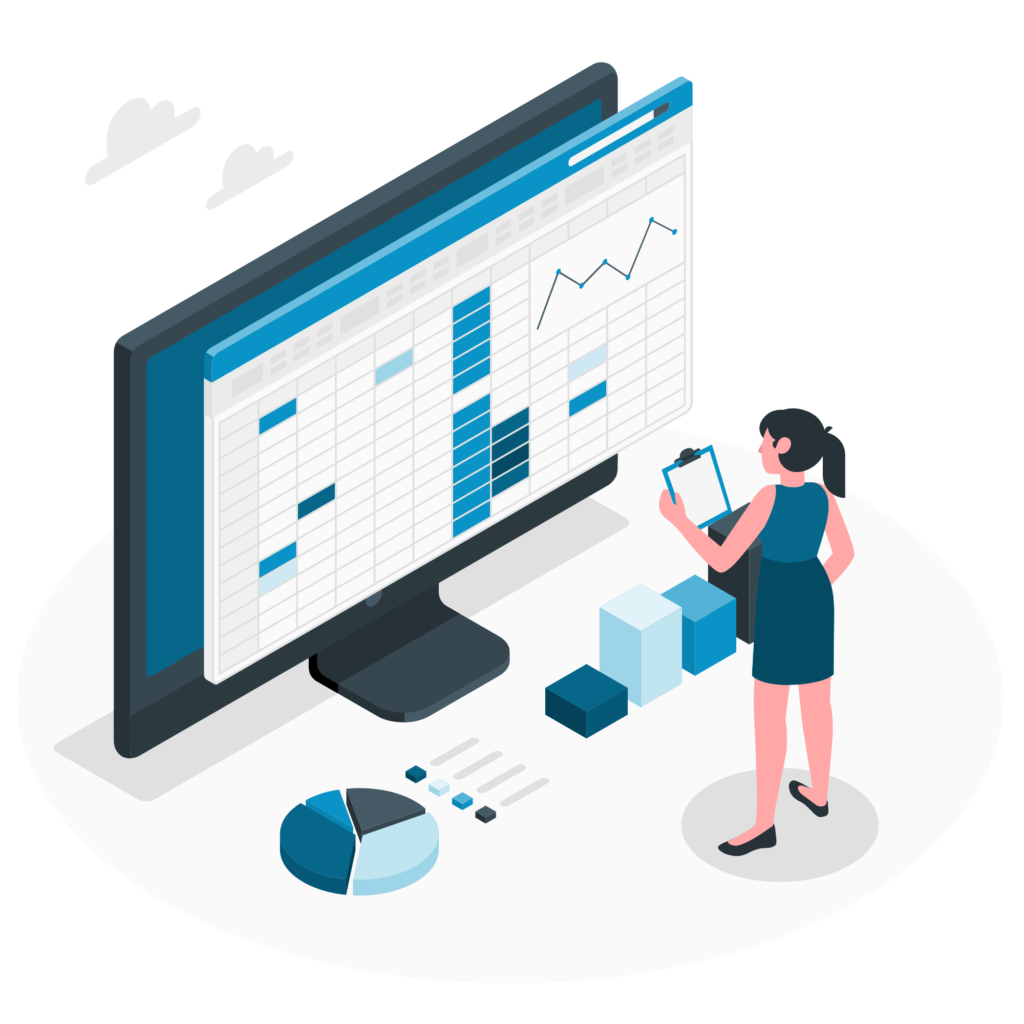
Step By Step Manufacturing Process
- Synergics– the best jewellery manufacturing software also supports manufacturing in all possible ways, including in-house manufacturing and subcontracting (RM / WIP handed to the job worker). Further, when it comes to subcontracting, it offers both full and partial subcontracting.
- The steps of in–house jewellery production are outlined below. However, the process flow can be customized to meet the requirements of the company.
- Following the approval of the sales order, the job bags or batch cards will be created and transferred to the wax injecting department for wax shooting.
- The stone control department will review the available inventory of stones for the orders.
- If there is no stock, the acquisition process will begin; otherwise, the stone control department will make the bunches of diamond bags.
- If the parts are to be wax studded, the wax injection department will transfer the batches with the wax models to the wax setting department. If not, the department will make the wax tree.
- The stone control department will transfer the bunches to the wax setting department, which will issue the wax models and bunches to the workers for wax setting.
- The batches will be returned to the worker after the wax setting.
- Following that, the wax setting department will transfer the batches for wax tree production as well as create the wax trees based on metal type, karat, and color.
- The metal control department will issue pure metal and alloy for alloying if the required alloyed metal is not available in stock, while the wax injecting department will transfer the wax tree to the casting department.
- The casting department will calculate the required alloyed metal per tree and inform the metal control department to issue the required alloyed metal. Note that all these operations will be performed using this online jewellery manufacturing software only.
- Using Synergics software for jewellery manufacturers, the metal control department will issue the required alloyed metal to the casting department, which will issue the wax tree and the required alloyed metal for casting.
- The casting department will weigh the casted tree and note the casting process loss.
- The department will then cut the tree and return the casted models, sprue metal candles, lose metal to the metal control department, and register the tree cutting loss.
- The metal control department will put the casted models in their respective job bags with their respective weights and transfer them to the filing department.
- The filing department will issue the job bags for different processes/operations like filing, linking, soldering, assembly, etc., and will issue extra metal, solder, wire to the worker.
- The filing department will take back the extra metal, sprue, solder, wire, etc., and register the process loss and transfer the job bags to the pre-polishing department.
- The pre-polishing department will issue job bags for the pre-polishing process, book the pre-polishing process's production, record the process loss, and transfer the job bags to the metal setting department.
- The metal setting department will issue job bags for either metal setting or wax setting finishing and book the metal setting process production and process loss before transferring the job bags to the final polish department, which will issue job bags for the polishing process.
- The final polish department will record the polishing process's production and the process loss and transfer the job bags to the QC department.
- The QC department will record the QC checking parameters for each job bag. If the QC department finds that something has to be repaired or modified, the QC department will have it repaired or modified through the respective department.
- Once the QC department has approved the pieces, they will be passed to the Finished Goods (FG) department.